AHCT GROUP NEWS
3PL Return Processing: How to Help Your Business
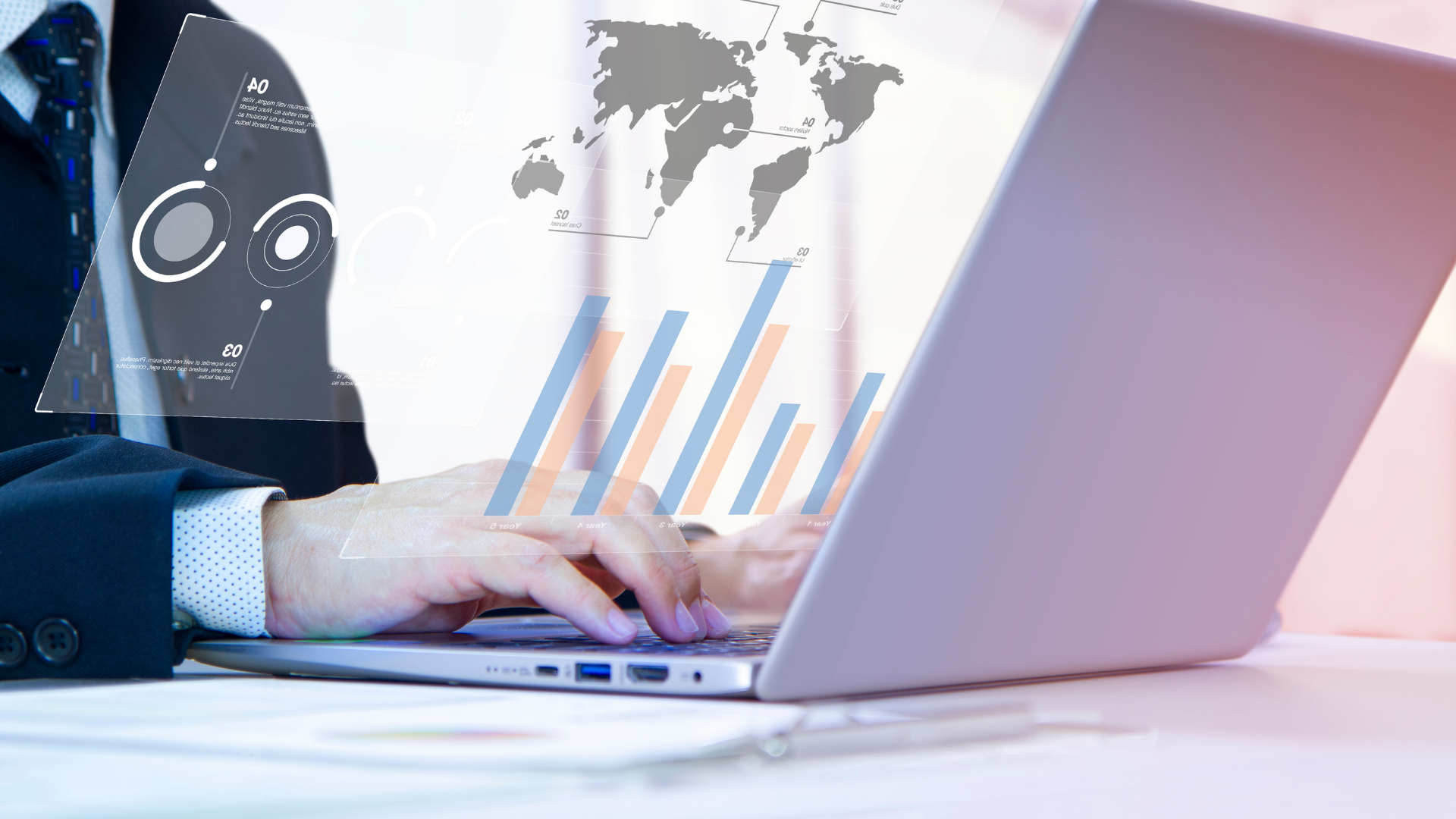
E-commerce sales are growing, reaching about $768 billion in 2021, but that means e-commerce returns are also rising. Return processing is an integral part of your e-commerce business. It is crucial to understand the process so that you can manage it well.
Each 3PL return processing center has its own policies and practices that may vary based on customer needs. This article will give you a basic idea of what to expect, as well as some examples of 3PL returns processing centers.
Step-by-step guide to returns processing
The 3PL return process begins when a customer initiates a return.
1. Create a Return Material Authorization
3PL uses a Return Material Authorization (RMA) form. Some return processing centers refer to this as a Return Material Authorization (RGA) or simply a Return Material Authorization (RA). You can also create an RMA using the online portal. The form tells the warehouse what to expect. It includes information such as customer name, authorized return date, order number, and carrier tracking number.
When the returned item arrives at the warehouse, we compare it to the RMA to make sure it matches. We then notify the customer that we have received the return.
2. Discard returned food
The next step in returns processing is to assess the condition of the returned item. However, if the return is for food, the return processing center does not need to inspect it. You must throw away food because you cannot sell returned food.
3. Check the package for damage
If a customer returns your product in the original box, the next step is to inspect the packaging for damage. It is not uncommon for product packaging to become dented, torn or otherwise damaged during round-trip shipping. This is especially true if the product is shipped in a package without an outer carton. Damaged packaging may also include torn plastic wrapping around the box.
Part of the buying experience that customers expect when purchasing a new product is "unboxing" it from its original packaging. As a result, companies often sell items with damaged boxes at a discount, even if the product is intact.
4. Put products in "new" status back into inventory
Items that can be resold as "new" should be back in stock shortly once the returns processing center has inspected the product. This is the ideal result for your business and returns processing center.
Your 3PL service provider can help you restore some products to like-new condition. For example, your 3PL warehouse can refold and repack unworn clothing. This will keep them neat, crisp and ready for the next buyer.
Return processing is often slower than order fulfillment. Returned products need to be inspected and handled individually. Additionally, returns may be slower during the coronavirus pandemic. While it's unlikely someone will catch the virus from touching the box, e-commerce fulfillment warehouses have had to implement new hygiene measures that could slow returns processing.
5.3 PL return flow example
The return process looks different for every business and every product. Ship large quantities of bulky products. These generally have lower return rates, but they are more likely to be returned with damaged packaging. This means that 3PL services have to be creative with returns handling.
When returning goods, 3PL will follow the specifications specified by the customer. If there are clear return instructions, the 3PL servicer will check with the customer before processing the return. A successful reverse supply chain puts as many returned items as possible online for resale.